The provisioning of therapeutic gases to infirmaries, mobile health suppliers, and in-patient care settings needs absolute conformance to strict industry canons. As a consequence, Medical Gas Pipeline System (MGPS) Manufacturers, suppliers, and facility safety bosses must have complete assurance of supply excellence and permanency.
It is vital to note that, while qualified governing organizations do set serious business fitness and safety rules, they neither assess nor review therapeutic gas apparatus, amenities, channels, or other substructures. Obedience is, therefore, the direct accountability of the therapeutic gas OEM, along with the discrete facility into which such airs are transported. To realize obligatory high-accuracy supervising and control, project engineers naturally stipulate pressure devices, buttons, and isolation faucets within finished system projects. For bigger or more compound schemes, they also subcontract the plan of bespoke manifolds. These assimilate devices, buttons, faucets, and other apparatuses into a single control unit.
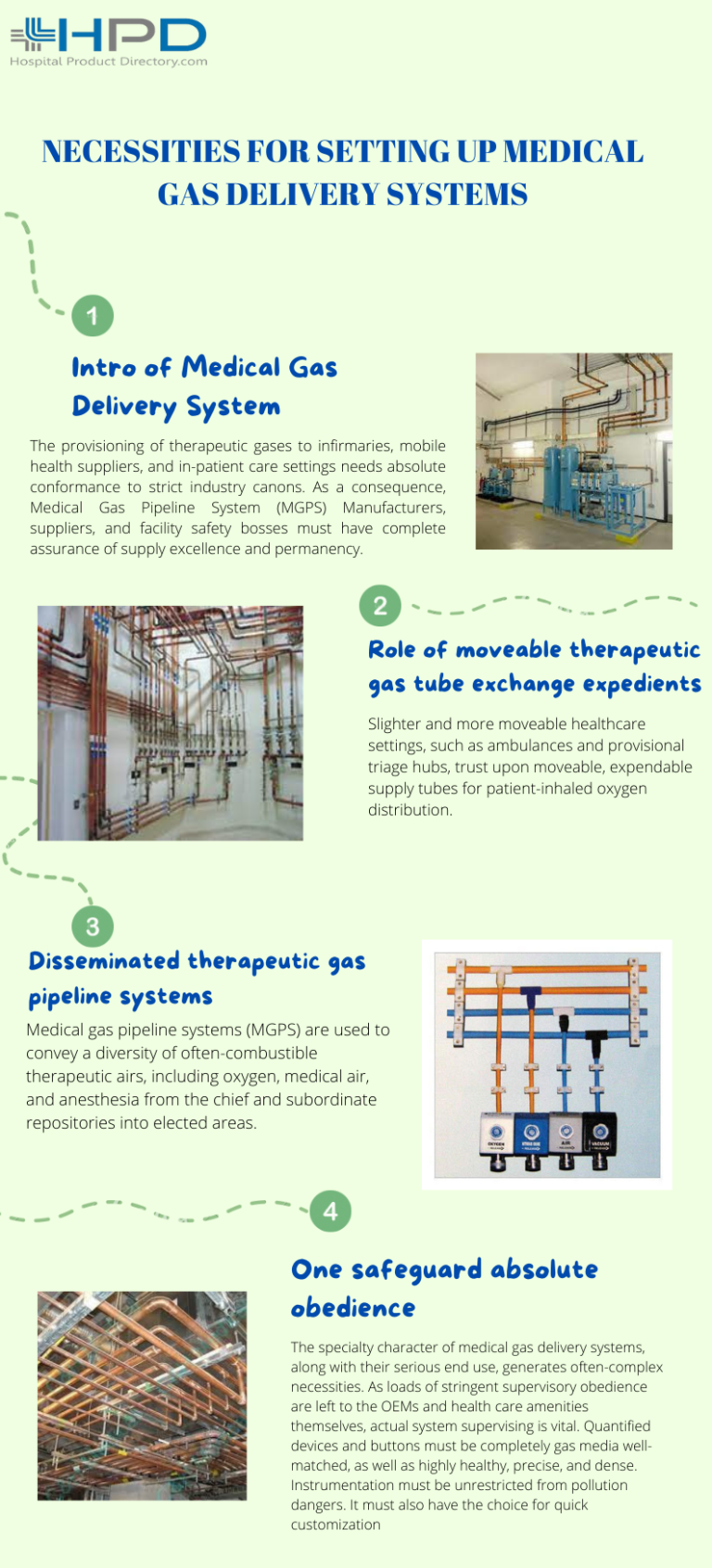
Requests that OEMs
naturally meet tackle the often-complex instrumentation necessities of medical
gas delivery schemes. These comprise the supervising of oxygen, helium, xenon,
carbon dioxide, and nitrous oxide; therapeutic and surgical air; and crushed
air vacuum schemes. Distinctive necessities can range anyplace from a few dozen
pressure buttons and faucets to the custom OEM volume engineering of fully
degreased, oxygen well-matched sensors, to the full instrumentation of medical
gas delivery tubes.
What is the role of
moveable therapeutic gas tube exchange expedients?
Without omission,
medical gas OEMs must stipulate instrumentation that is in strict conformance
with the all-out permissible and constancy absorptions of transported patient
oxygen. Slighter and more moveable healthcare settings, such as ambulances and
provisional triage hubs, trust upon moveable, expendable supply tubes for
patient-inhaled oxygen distribution.
Due to the wide
peripheral temperature choices over which moveable switch systems must
function, cylinder arrangements are also instrumented with security alarms. High-pressure
alarms gesture advanced temperatures and amplified danger of gas store
reduction produced by vaporization. Low-pressure alarms can gesture awaiting
cylinder switch necessities.
Pressure observing
ranges differ, contingent upon the medical gas kind. Thus, careful courtesy to
correct sensor selection standards is vital. Quantified instrumentation can
precisely screen the tube pressure levels of oxygen, nitrous oxide, and other
therapeutic gases. Naturally connected between the tubes and gas delivery
scheme, they also help to regulate correct cylinder stock exchange criteria and
judgment. One transducer is used to gauge inward transported gas supply
pressure. Another gauge supplies forage pressure to the delivery system. This
method safeguards that consistent pressure levels are upheld inside a stated
variety.
Therapeutic grade
pressure knobs are also connected on cylinder alarms to deliver actual early
threats of conceivable supply system jeopardies, as well as seepages or
obstructions. They are also used to ease the switch of tubes from reserve to
on-duty styles. Comprehensive pressure manifolds, containing a pressure button
and various separation regulators, are also quantified for these
requests.
How are medical air
generation compressors and vacuum systems useful in these pipelines which are
supplied by the Medical Gas Pipeline System (MGPS) Suppliers?
Surgical and
therapeutic air is vital for harmless operating theatre, patient infirmary
ward, and intensive care component functionality. Trodden air aids therapeutic
professionals to transport appropriate surgical anesthesia and gulped patient
oxygen absorptions. It also controls investigative and operating apparatus,
dental tools, and other non-critical therapeutic devices.
Medical and surgical
air is naturally shaped via subject water- or air-cooled compressor schemes. To
keep on active, a compressor must be spotless and dehydrated, as well as remain
dust-, mold-, and oil-free through its process. It also must be dependably
accomplished to change set pressure stages. To safeguard this, compressors are
instrumented with both an instinctive manifold board and a manifold standby,
each automated to a predefined set cushion pressure array. In the occurrence
that an instinctive manifold is fatigued, a subordinate spare standby manifold
involves, safeguarding continuous airflow. Both manifolds necessitate precise,
incessant pressure level observing.
Strong-featured
stainless-steel pressure devices are often quantified inside these producer
schemes. The devices form a portion of a control trip that triggers and
neutralizes the compressor, permitting it to mechanically screen source
pressure. In doing so, they aid to safeguard that shield pressure remains
inside its predefined set variety. These devices can dependably function over a
diversity of pressure locations, with low thermal mistakes and an extensive
temperature recommended range. Devices may also be modified with
application-specific pressure varieties, ports, connectors, chains, and
electrical yields. In addition, the devices can act as an alarm, offering early
notice must echelons fall below satisfactory standards. Information from these
devices also delivers important general compressor health calculations.
What is the use of
disseminated therapeutic gas pipeline systems?
Medical gas pipeline
systems (MGPS) are used to convey a diversity of often-combustible therapeutic
airs, including oxygen, medical air, and anesthesia from the chief and
subordinate repositories into elected areas. Stereotypically built of copper,
MGPS boost high- and low-pressure therapeutic gas delivery inside infirmaries,
laboratories, and other medical settings.
Rudimentary medical
gas pipeline substructure contains a chief line linking the gas media supply to
the risers; risers, which attach the chief line to adjacent tubes; and adjacent
tubes, which feed into a subdivision room or set of rooms, inside the
therapeutic care setting. These tubes are connected inside the care location in
unadorned view, versus behind walls.
All MGPS bought
from Medical
Gas Pipeline System (MGPS) Dealers must be widely
verified before use. This is to safeguard acceptable gas delivery pressure,
supply guideline, and control. Mainly, gas provisions to anesthesia respirators
are most serious, as those trust upon adequately high-pressure stages for
appropriate functionality. To safeguard such functionality, MGPS must also be
unceasingly checked for pressure and temperature differences and excesses.
Devices applied inside these settings are used to deliver critical early
warning of imminent pressure descents or overpressure circumstances.
The highly scarring
nature of sure gas media makes MGPS disposed to erosion, dampness, mildew,
pressure anxieties, and other mechanical indemnities. Over time, these issues
can underwrite to pipe escapes. Inside an oxygen distribution setting, such
escapes can stance an expressly high risk of fire or burning, as well as
patient health injury caused by exhausted oxygen supplies. Instrumentation
necessities call for the supervising of separate pipelines, with their
stipulations founded upon the kind of calculated gas media and unused emergency
supplies.
How does one
safeguard absolute obedience?
The specialty
character of medical gas delivery systems, along with their serious end use,
generates often-complex necessities. As loads of stringent supervisory
obedience are left to the OEMs and health care amenities themselves, actual
system supervising is vital. Quantified devices and buttons must be completely
gas media well-matched, as well as highly healthy, precise, and dense.
Instrumentation must be unrestricted from pollution dangers. It must also have
the choice for quick customization.